Redundant Robot
Hyper-redundant multi-joint robots have very high relative degrees of kinematic redundancy. These robots, which are analogous in design and operation to the “trunk of an elephant”, have unconventional features such as the ability to enter narrow spaces while avoiding obstacles. They thus can be used not only for industrial applications but also applications where a conventional industrial robot could not be introduced. The realization of such a hyper-redundant multi-joint robot is difficult because of serious engineering problems involved. One problem is a very limited ratio of output to its own weight. A multi-degrees-of-freedom driving mechanism mounted on the arm makes the robot arm quite heavy. A powerful driving system needed to support such a long and heavy arm makes the arm even heavier. Another problem is how to resolve their redundancy and control them in real-time. To solve these problems and realize an applicable hyper-redundant robot, we have provided new designs and control methods including a biologically inspired control method to resolve redundant degrees of freedom.
Snake-like robot
With slim and legless body, particular ball articulation, and rhythmic locomotion, a nature snake adapted itself to many kinds of terrains: rough surfaces; narrow pathways; soft grounds; underwater. By applying these advantages, snake-like robot can be expected to do search or rescue tasks in the unstructured environment where wheeled or legged robots cannot move well.
Biological snakes’ diverse locomotion modes and physiology make them supremely adapted for environment. When their unique movements are broadly classified, the following four gliding modes exist: 1) Serpentine locomotion; 2) Rectilinear locomotion; 3) Concertina locomotion; 4) Side winding locomotion. However, the serpentine locomotion is the movement seen typically in almost all kinds of snakes, its characteristic is that each part of the body leaves similar tracks. All above indicate that snakes’ locomotion is a kind of rhythmic locomotion, they are the perfect combinations of simplicity and practicality. Thus, the control method of imitating snakes’ rhythm locomotion is often adopted to actualize the locomotive function of a snakelike robot. Ma put forward the Serpentine curve which is more valid as the snake creeping locomotion shape than the previously suggested Clothoid spiral, the Serpenoid curve, and others.
During the process of progressing, the elongated body of snake-like animals is smooth and of elliptical cross-section, so that the friction coefficient in the normal direction is significantly greater than the tangential one. By use of a passive wheel on snake-like robot we can imitate this biological characteristic. The propelling force of the serpentine motion of a snake-like robot comes from the interaction of the robot with the ground by swinging the joints from side to side. Each modular of the snake-like robot is composed of two motors which are used for yaw rotation and pitch rotation.
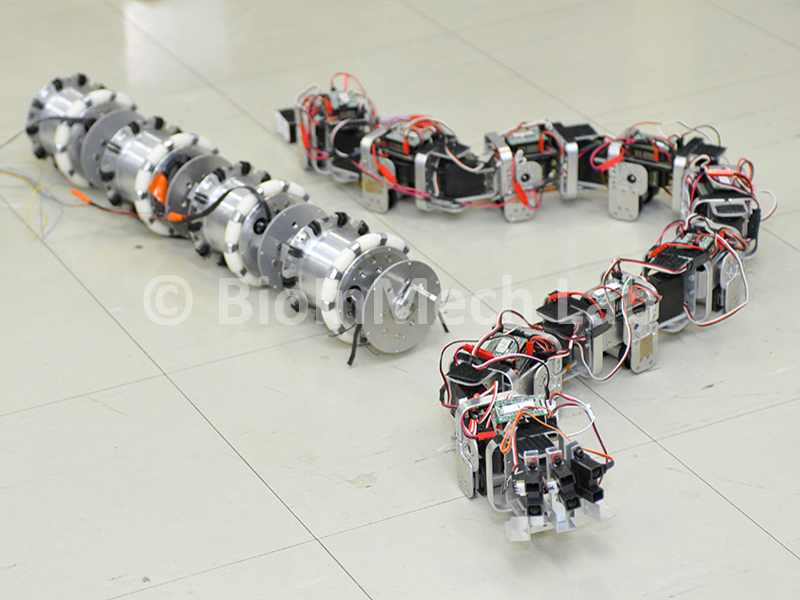
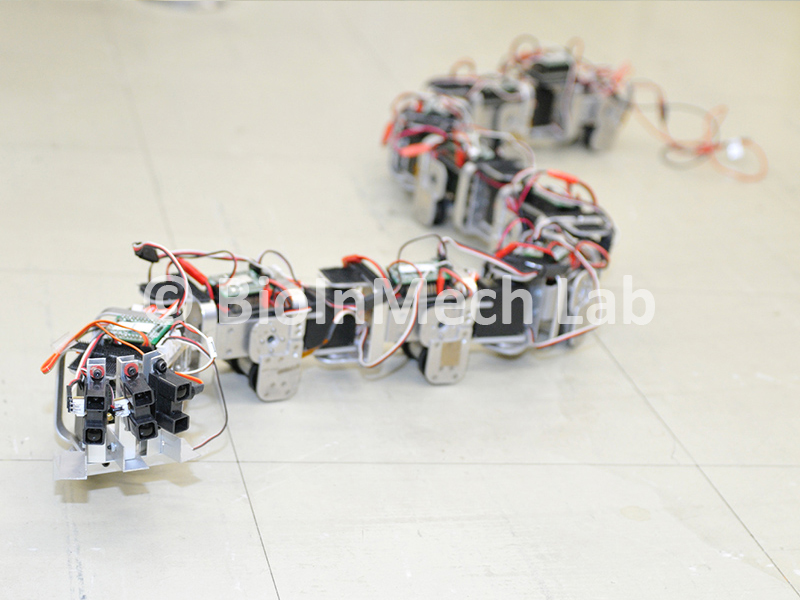
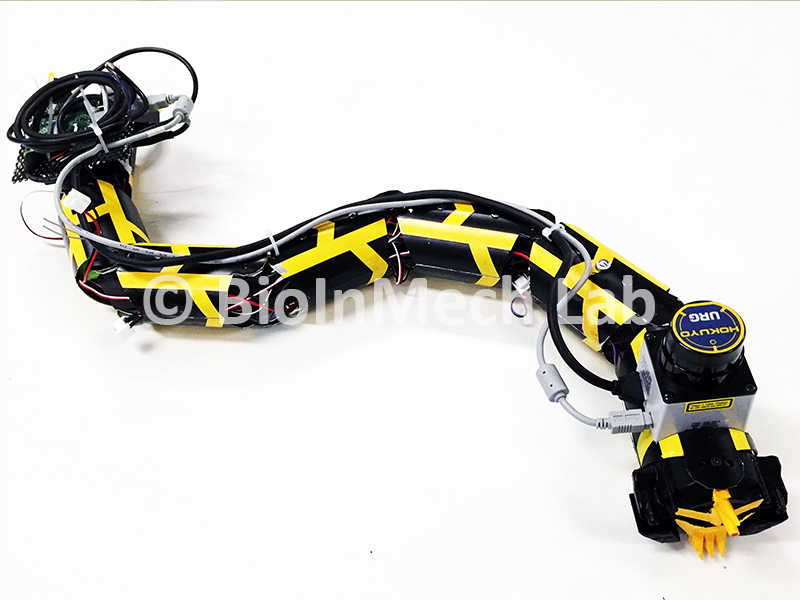
- Shugen Ma. Analysis of Creeping Locomotion of a Snake-like Robot. Int. J. of Advanced Robotics. 2000
- Shugen Ma, Yoshihiro Ohmameuda and Kousuke Inoue. Dynamic Analysis of 3-dimensional Snake Robots. In Proc. 2004 IEEE/RSJ Int. Conf. on Intelligent Robots and Systems (IROS’04), pp. 767-772, Sendai, Japan, 2004
Hyper-redundant manipulators: coupled tendon-driven mechanism
A multi-joint manipulator just like trunk of elephant has unconventional features such as to go inside narrow space while avoiding obstacles. It is thus suitable for the various applications where conventional industrial robot could never been introduced. However, realization of such a multi-joint manipulator was not easy for there were serious engineering problems. The biggest problem among them might be that of weight. A multi-degree of freedom driving mechanism mounted on the arm made the whole manipulator considerably heavy. Powerful driving system to support such long and heavy arm made the arm all much heavier. On this account, a multi-joint manipulator was regarded unfeasible unless very compact, light-weight and powerful actuators were developed.
Therefore, mechanism of the coupled tendon-driven manipulator, called CT arm, has been proposed by us. The proposed CT arm is based on the design concept of mechanism referred to as the coupled drive and connected differential mechanism. The developed manipulator (CT arm) has the specific tendon traction force transmission mechanism, in which a pair of tendons to drive a joint are pulled from base actuators via pulleys mounted on the base-side joints. The mechanism makes the most of coupled drive function of the tendon traction forces and thus has a possibility to exhibit enormous payload capability in light weight of the manipulator arm. CT arm also has characteristics to be solidly structured and to be inexpensively manufactured because of its mechanical simplicity.
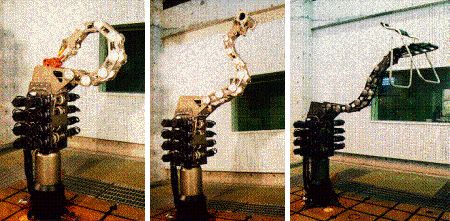
- S. Ma, S. Hirose, and H. Yoshinada. Design and Experiments for a Coupled Tendon-driven Manipulator, IEEE Control Systems Magazine, 1993
- S. Ma. A New Formulation Technique for Local Torque Optimization of Redundant Manipulators. IEEE Trans. on Industrial Electronics, 1996
- Shugen Ma, Isao Kobayashi, Shigeo Hirose, and Kiyoshi Yokoshima. Development of a Multijoint Manipulator: Moray Arm. IEEE/ASME Trans. on Mechatronics, 7-3, pp. 304-317 2002.9
- Shugen Ma and Mitsuru Watanabe, Minimum Time Path-tracking Control of Redundant Manipulators. JSME Int. Journal, Series C: Dynamics, Control, Robotics, Design and Manufacturing, 47-2, pp. 582-590, 2004.6
Moray arm: slider-installed robot arm
Kinematically redundant manipulators have been receiving an increasing attention because of their ability to perform tasks of high complexity. Besides the end-effector task, one or more additional tasks can be accomplished. Therein, the end-effector motion of the redundant manipulator was given as a primary task and the subtask like the avoidance of singularities, obstacles, or joint limits, the minimization of joint velocities, or joint torques, etc. was performed at same time. However, how to use the redundant degrees of freedom of the manipulator to increase the path-tracking velocity or to make the manipulator track the geometric path in minimum time, in subjection to joint torque limits, was never discussed. In our study, we proposed a time-optimal control scheme for kinematically redundant manipulators to track a pre-defined geometric path, subject to joint torque limits. The scheme makes full use of redundancy to increase the path-tracking velocity, and the time-optimal trajectory planning problem was solved by using the phase-plane analysis and the linear programming technique.
