Pipeline Inspection Robot
Articulated Wheeled Pipeline Inspection Robot: AIRo series
We designed a multilink-Articulated Inspection Robot with omni and hemispherical wheels (AIRo-II). A pair of the hemispherical wheels was attached at the end of the robot. They freely rotated in the traveling direction and driven around the link axis by a motor.
For the holonomic rolling movement in the pipe, it was necessary to replace driving actuators with rolling actuators at the expense of the driving force. In our case, there were four housings that could be mounted on the actuators; however, two of the housings must be replaced with rolling actuators. Additionally, if the joint actuation could be replaced by the torsion spring, both the total weight and the cost of the robot could be reduced. Thus, maintenance becomes easier. Therefore, we pursued the possibility of achieving high maneuverability in the winding pipes with only two driving actuators and springs for body bending.
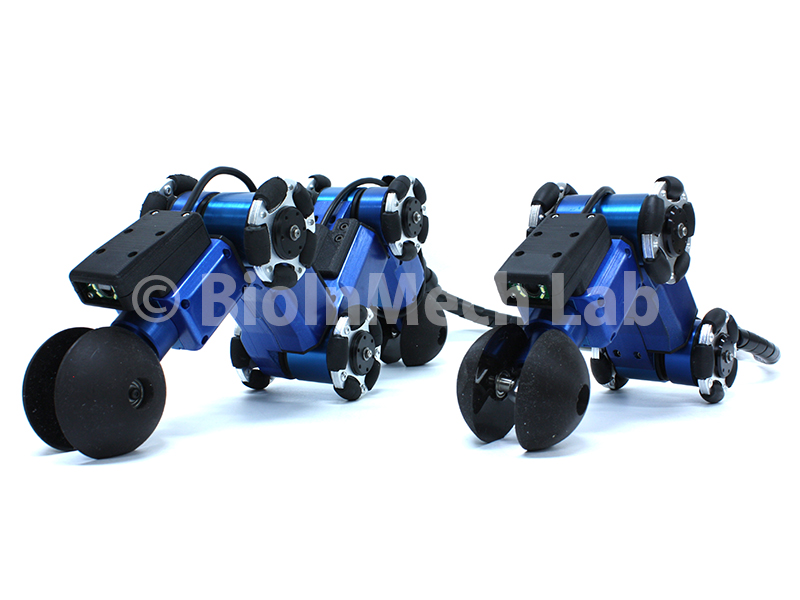
- Atsushi Kakogawa, Yuki Komurasaki, and Shugen Ma, Shadow-based Operation Assistant for a Pipeline-inspection Robot using Variance of Pixel-number to the Luminance, Journal of Robotics and Mechatronics, 31-6, pp. 772-780, 2019.
- Atsushi Kakogawa and Shugen Ma, Design of a Multilink-articulated Wheeled Pipeline Inspection Robot using Only Passive Elastic Joints, Advanced Robotics, pp. 1-14, 2017, 10.1080/01691864.2017.1393348, Published Online.
[References]
- G. C. Vradis and W. Leary, Development of an Inspection Platform and a Suite of Sensors for Assessing Corrosion an Mechanical Damage on Unpiggable Transmission Mains, Technical Report of NGA and Foster-Miller, 2004.
- E. Dertien, S. Stramigioli, and K. Pulles, Development of an Inspection Robot for Small Diameter Gas Distribution Mains, in Proc. the IEEE Int. Conf. Robotics and Automation, pp. 5044-5049, 2011
- P. Debenest, M. Guarnieri, and S. Hirose, PipeTron Series - Robots for Pipe Inspection, in Proc. of the 3rd Int. Conf. Applied Robotics for the Power Industry, pp.1-6, 2014.
- K. Tadakuma, Tetrahedral Mobile Robot with Novel Ball Shape Wheel, in Proc. the First IEEE/RAS-EMBS Int. Conf. Biomedical Robotics and Biomechatronics, pp. 946-952, 2006.
- K. Tadakuma, R. Tadakuma, and J. Berengeres, Development of Holonomic Omnidirectional Vehicle with "Omni-Ball": Spherical Wheels, in Proc. the IEEE/RSJ Int. Conf. Intelligent Robots and Systems, pp. 33-39, 2007.
Torque-sensible Active Joint
This robot module can control its joint angle and torque and adapt to any directed bent pipe regardless of its orientation. Stretching the drive wheels against the inner wall of pipes is essential for adapting robots to be used in vertical pipes and slippery inner surfaces. To achieve this, a series elastic actuator (SEA) with a high reduction system and a polyurethane rubber spring is installed to sense the joint torque. More than approximately 200 N (20 kgf) constant traction force and a wide range of adaptive inner diameters (4 to 6 in.) are achieved despite the short body length, a minimum number of the drive wheels, and a simple joint of 1 degree of freedom.
Furthermore, the remarkable feature of this mechanism is that it can pass through even a vertical T-branch pipe (including those with zero radius of curvature). AIRo-5.1, which consists of only one active joint and two passive compliant joints, succeeded the travel though vertical T-branches by controling the angle along the cosine wave trajectory without adding motors to all three joints.
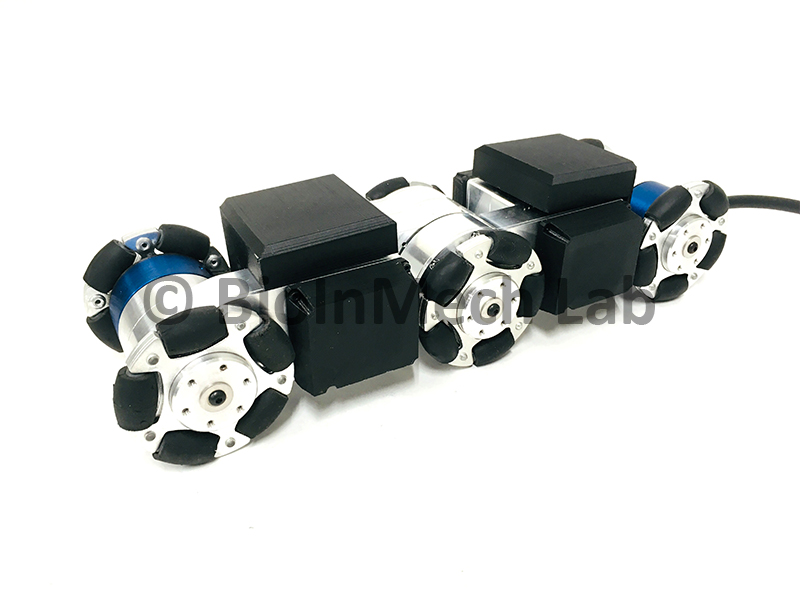

- Atsushi Kakogawa and Shugen Ma, A Multi-link In-pipe Inspection Robot Composed of Active and Passive Compliant Joints, IEEE/RSJ Int. Conf. Intelligent Robots and Systems (IROS 2020), pp. 6472-6478, 2020, Las Vegas, USA (Virtual).
- Atsushi Kakogawa and Shugen Ma, An In-pipe Inspection Module with an Omnidirectional Bent-pipe Self-adaptation Mechanism using a Joint Torque Control, IEEE/RSJ Int. Conf. Intelligent Robots and Systems (IROS 2019), pp. 4347-4352, 2019, Macau, China.
- Atsushi Kakogawa and Shugen Ma, Differential Elastic Joint for Multi-linked Pipeline Inspection Robots, IEEE/RSJ Int. Conf. Intelligent Robots and Systems (IROS 2018), pp. 949-954, 2018, Madrid, Spain.
[References]
- D. Rollinson, S. Ford, B. Brown, and H. Choset, Design and Modeling of a Series Elastic Element for Snake Robots, in Proc. the ASME Dynamic Systems and Control Conference, pp. 1-5, 2013.
- D. Rollinson, Y. Bilgen, B. Brown, F. Enner, S. Ford, C. Layton, J. Rembisz, M. Schwerin, A. Willig, P. Velagapudi and H. Choset, Design and Architecture of a Series Elastic Snake Robot, in Proc. the IEEE/RSJ Int. Conf. Intelligent Robots and Systems, pp. 4630-4636, 2014.
Shadow-based Operation Assistant System to Pass through Bent Pipes
In this study, we propose an anisotropic shadow-based operation assistant method for a multilink-articulated wheeled pipeline-inspection robot by using a single illuminator and camera. By displacing the position of the illuminator relative to that of the head camera, a crescent-shaped shadow appears in the images captured in a bent pipe. The size, position, and orientation of the shadow depend on the robot orientation around the pipe axis, and the shadow disappears in a certain robots orientation (anisotropic shadow). Our developed robot (AIRo-2) adapts to a bent pipe without any control when the robot orientation and the pathway direction of the bent pipe are aligned. By aligning those two specific orientations, we developed operation assistant system to pass through winding pipes.
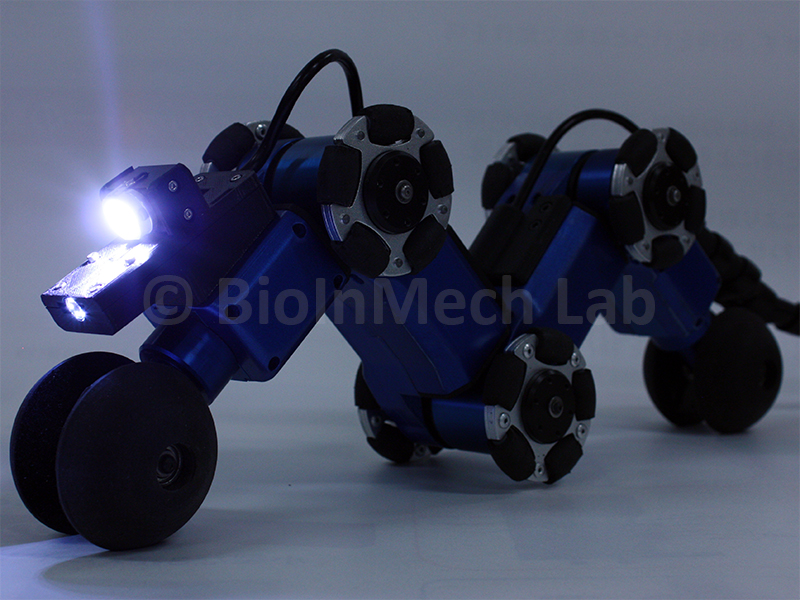
- Atsushi Kakogawa, Yuki Komurasaki, and Shugen Ma, Shadow-based Operation Assistant for a Pipeline-inspection Robot using Variance of Pixel-number to the Luminance, Journal of Robotics and Mechatronics, 31-6, pp. 772-780, 2019
- Atsushi Kakogawa, Yuki Komurasaki and Shugen Ma, Anisotropic Shadow-based Operation Assistant for a Pipeline-inspection Robot using a Single Illuminator and Camera, in Proc. 2017 IEEE/RSJ International Conference on Intelligent Robots and Systems (IROS2017), pp. 1305-1310, 2017, Vancouver, Canada.
Three module pipeline inspection robot
The increase in the number of actuators and sensors leads to an increase in the size, weight, and operation difficulty of the robot. Therefore, we propose a new inpipe robot with three underactuated parallelogram crawler modules. It can automatically adapt to the diameter change and inner obstacles without any additional active arms. The newly developed in-pipe robot consists of three underactuated parallelogram crawler modules that are radially connected with an interval of 120 degree. Each underactuated parallelogram crawler module consists of an underactuated parallelogram mechanism and a foldable mechanism. We used the parallelogram for two reasons. First, the length of the belt is constant even when the crawler’s shape is transforming; thus, the robot requires no additional mechanism to adjust the belt length. Secondly, the anterior-posterior symmetric transformation can be easily realized.
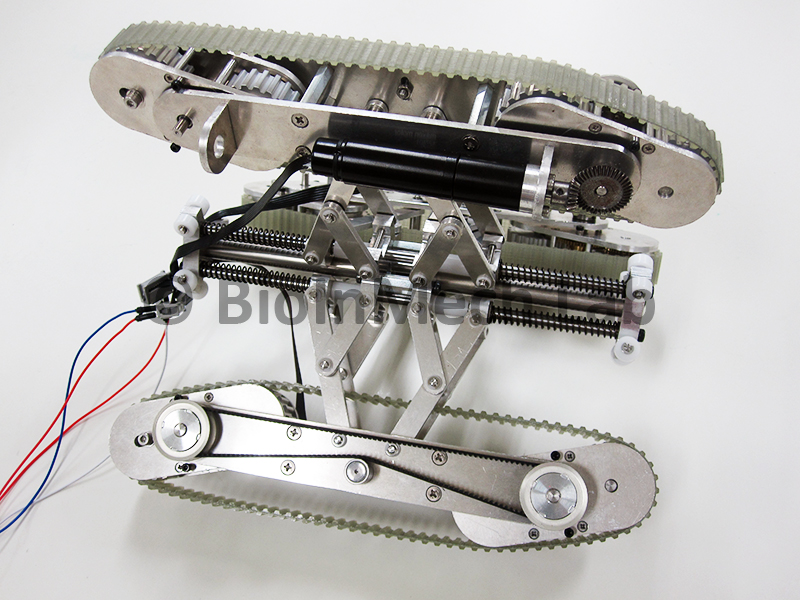
![]() |
![]() |
(1) Output gear rotates (Blue) | (2) Output gear revoluves (Green) |
- Atsushi Kakogawa and Shugen Ma, Speed Analysis of Three Driving Modules for an In-pipe Inspection Robot to Pass through a Bent Pipe, in Proc. The IEEE Int. Conf. Robotics and Biomimetics (ROBIO2014), pp.1731-1736, 2014.12, Bali, Indonesia
- Atsushi Kakogawa, Shugen Ma, and Shigeo Hirose, An In-pipe Robot with Underactuated Parallelogram Crawler Modules, in Proc. The IEEE Int. Conf. Robotics and Automation (ICRA2014), pp.1687-1692, 2014, HongKong, China
- Atsushi Kakogawa and Shugen Ma, Design of an Underactuated Parallelogram Crawler Module for an In-pipe Robot, in Proc. The IEEE Int. Conf. Robotics and Biomimetics (ROBIO2013), pp. 1324-1329, 2013, Shenzhen, China
Screw drive pipeline inspection robot
The robot comprises three units: a front-rotating unit (rotator), a middle-steering unit, and a rear-supporting unit (stator). The front and rear units have three elastic arms, which can be elongated by springs. The arms can push against the inner wall of the pipe to support the robot. The end of each arm has a pair of passive wheels. The wheels of the front unit are angled with respect to the pipe's cross-section. When the motor turns, the wheels of the front unit rotate not only around their own axes but also around the axis of the pipe. At a branch pipe, the robot can swing its front unit toward the next desired direction using a steering motor. For example, if the swing direction is up-and-down at a T-branch that branches to the right or left direction (i.e., the swing and pathway directions are different), the middle unit can roll around the pipe-axis for changing the swing direction. These movements are generated by a differential mechanism. Using this mechanism, the robot can travel and steer not only in straight pipes but also through bent pipes and T-branches.
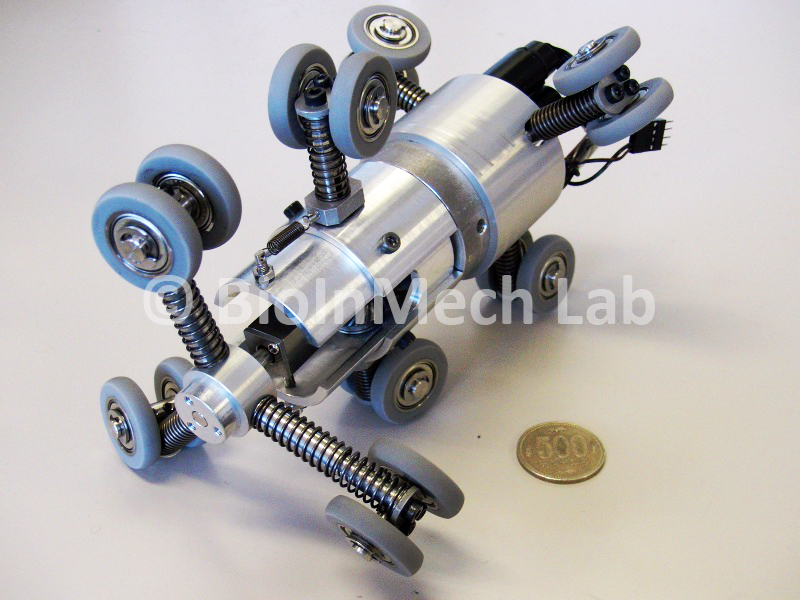
![]() |
![]() |
(1) Output gear rotates (Blue) | (2) Output gear revoluves (Green) |
- Atsushi Kakogawa, Taiki Nishimura, and Shugen Ma, Designing Arm Length of a Screw Drive In-pipe Robot for Climbing Vertically Positioned Bent Pipes, Robotica, Published Online, 2014/06
- Atsushi Kakogawa and Shugen Ma, Stiffness Design of Springs for a Screw Drive In-pipe Robot to Pass through Curved Pipes and Vertical Straight Pipes, Int. J. of Advanced Robotics, 26-3/4, 2012.2, pp.253-276
- Taiki Nishimura, Atsushi Kakogawa and Shugen Ma, Pathway Selection Mechanism of a Screw Drive In-pipe Robot in T-branches, in Proc. 8th IEEE International Conference on Automation Science and Engineering (CASE2012), 2012.8, pp.612-617, Seoul, Korea